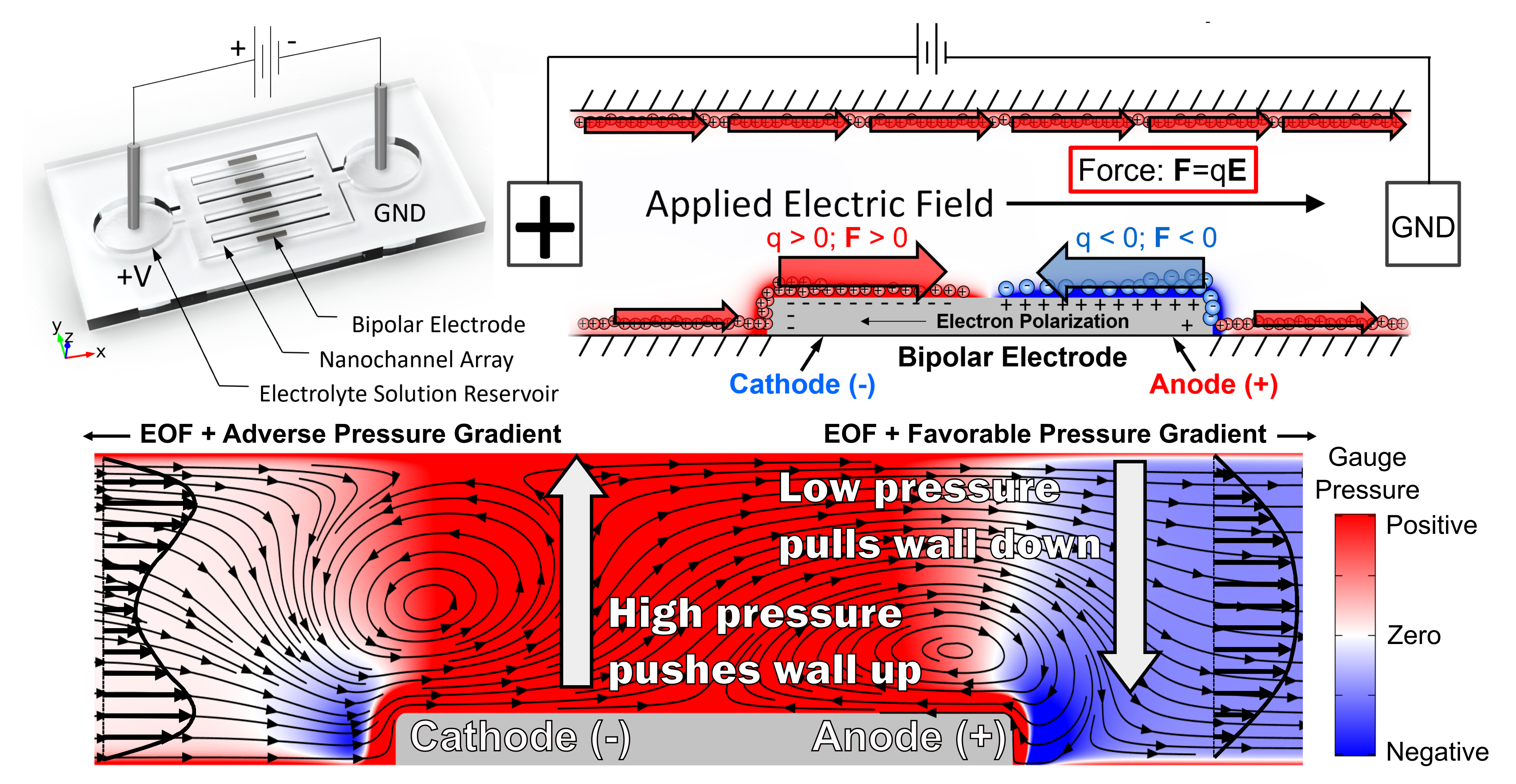
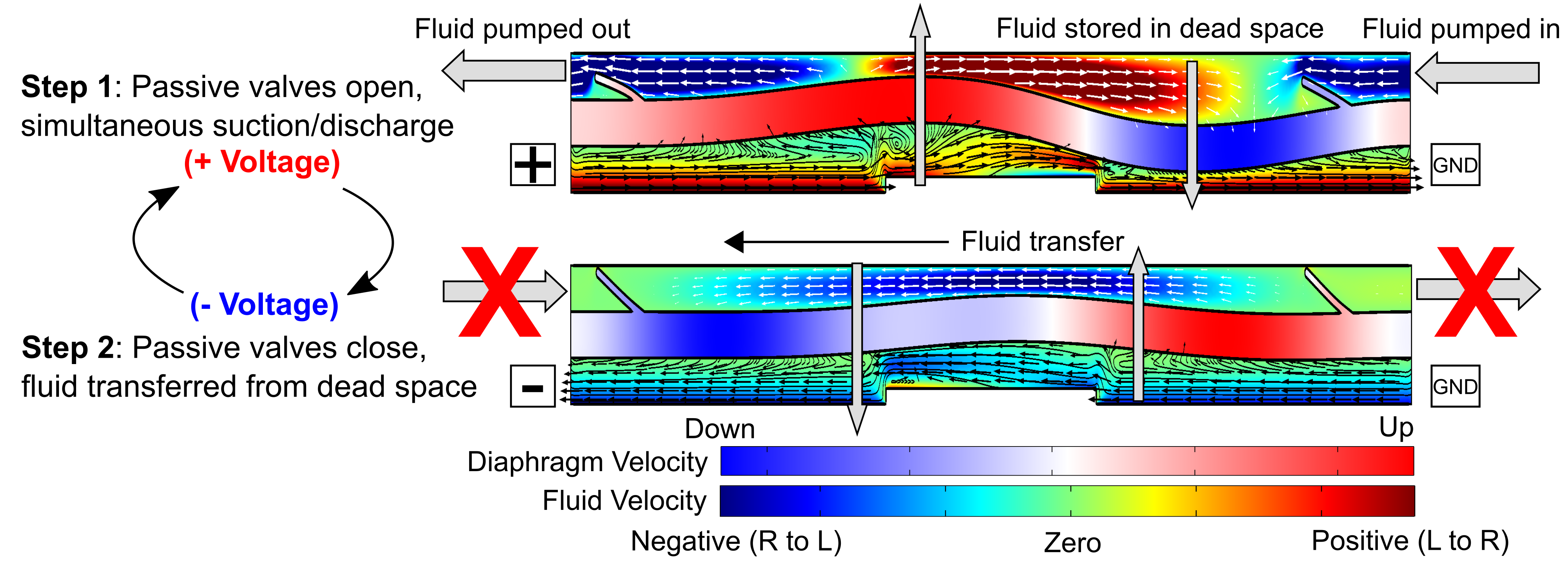
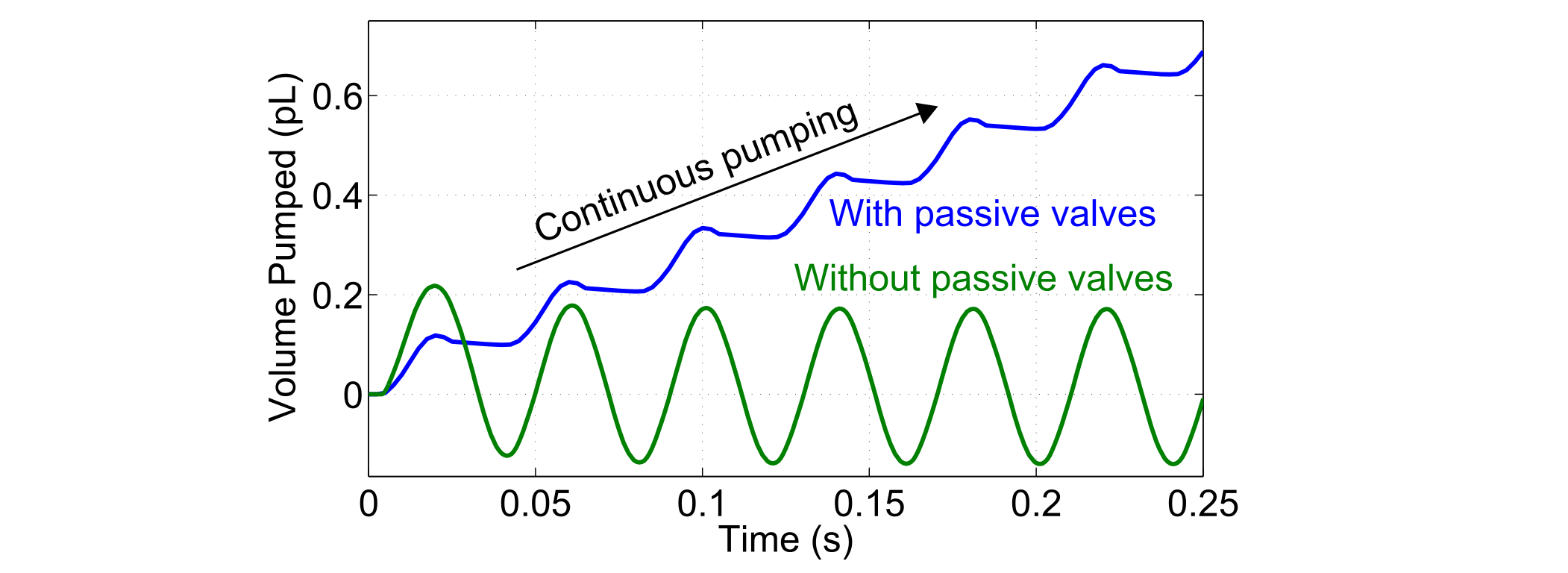
The ideal insulin pump will be small, low-power, and precise. We propose a microfluidic approach to insulin delivery that offers the promise of seamless integration into a hybrid fluidic drug delivery system. Our electrokinetic approach is built on the premise of nonuniform induced-charge electroosmotic flow (ICEOF) in confined geometries. When an electronically isolated conductor is exposed to an applied electric field inside a fluidic channel, freely mobile electrons in the conductor internally redistribute so as to be closer to the region of highest fluid potential (i.e. electrons accumulate at the left end of the electrode in Figure 1). This field-induced charge polarization leads to the formation of two oppositely charged “poles” at the extremities of the electrode, as well as the formation of charge-screening electrical double layers (EDLs) in the adjacent solution phase. These oppositely charged “ionic clouds” above the bipolar electrode (BPE) poles experience opposing electrical forces under the axial electric field and are subsequently transported in opposite directions, leading to fluid recirculation in the region above the BPE. This ICEOF is accompanied by pressure disturbances in the fluid, which we have recently found to be theoretically capable of appreciably deforming a thin (~ 10 μm) diaphragm made of a flexible polymer material such as polydimethylsiloxane (PDMS) or neoprene [1].
In light of this discovery, we devised a hypothetical pumping configuration consisting of two channels separated by a flexible diaphragm: a top channel containing the sample fluid to be pumped, and a bottom actuation channel in which the BPE is located and the electric field is applied to generate the ICEOF-related pressure forces. When a positive voltage is applied across the channel, the combined effect of ICEOF at the BPE and background EOF (an artifact of intrinsically charged channel walls) cause the diaphragm to deflect upwards at the left BPE pole and downwards at the right BPE pole. This deflection displaces the bottom boundary in the top channel, expelling fluid out of the left boundary while simultaneously drawing in fluid at the right boundary. When the polarity of the applied voltage is switched, the displacement directions reverse and fluid in the top channel naturally tends to move in the opposite direction; however, by integrating angled polymer flaps to act as passive valves and inhibit backflow, the flow direction can be rectified and fluid can be pumped in a single direction over time. Figure 2 depicts numerical simulation results at the two voltage extremes during sinusoidal AC actuation and illustrates the flow rectification from the passive valves. These results demonstrate the precise, unidirectional pumping of an isolated fluid with incredibly small power requirements per pumping channel (~ 100 nW). The device footprint (~ mm long/wide channels) is highly amenable to parallelization, allowing for scalable flow control across multiple fluidic platforms.
References:
[1] Eden, A., Scida, K., Arroyo-Currás, N., Eijkel, J.C.T., Meinhart, C.D., Pennathur, S. (2019). Modeling Faradaic Reactions and Electrokinetic Phenomena at a Nanochannel-Confined Bipolar Electrode. Journal of Physical Chemistry C, 123 (9), 5353-5364.